Interview with Yousef Imani, Eng., Ph.D., Project director of numerical simulation, Merkur Inc.
Numerical simulation, often called finite element analysis (FEA), allows you to effectively represent the mechanical, thermal, and other behaviours of your products. It allows you to visualize and better understand the behavior of a part or an assembly before manufacturing it. At Merkur, we are fortunate to have a specialist in this field: Yousef Imani, P.Eng., Ph.D. Possessing a Ph.D. in mechanical engineering from Laval University and extensive experience in numerical simulation in the fields of transport and aeronautics, Yousef has been in charge of the development of the simulation team at Merkur since November 2021. As a project director, he leads a team that could become your best friend. Let’s understand why…
ALSO TO BE READ: visit our page dedicated to numerical simulation (FEA)
Why is FEA expertise valuable for product optimization?
Yousef Imani: “Thanks to our expertise in numerical simulation, you have the opportunity to invest in an optimal product and reduce product development costs and time. You also increase your chances of succeeding the first time. Throughout your project, we support you to better understand your problem. For example, we validate concepts with analytical and numerical calculations before making recommendations. With us, you will be able to better understand the issues related to loading and constraints before you start manufacturing your product.
With the expertise in simulation acquired throughout my career, I had the opportunity to carry out static and dynamic analysis which determine the resistance of a product to the various load cases during its life cycle. These analyses make it possible to evaluate the reaction forces, the safety factors, as well as the possible deformations.
By working on various simulation projects, I have notably developed an expertise in the evaluation of load cases, which allows me to properly model a product’s performance. Then, with the acquisition and processing of experimental data, the results of the simulations can be compared, and I can thus ensure the correlation between them. This ensures that the numerical analysis will accurately represent the actual performance of the product throughout its life cycle. As simulation applies to different sectors of activity (automotive, aeronautics, medical, etc.), its usage has great potential.”
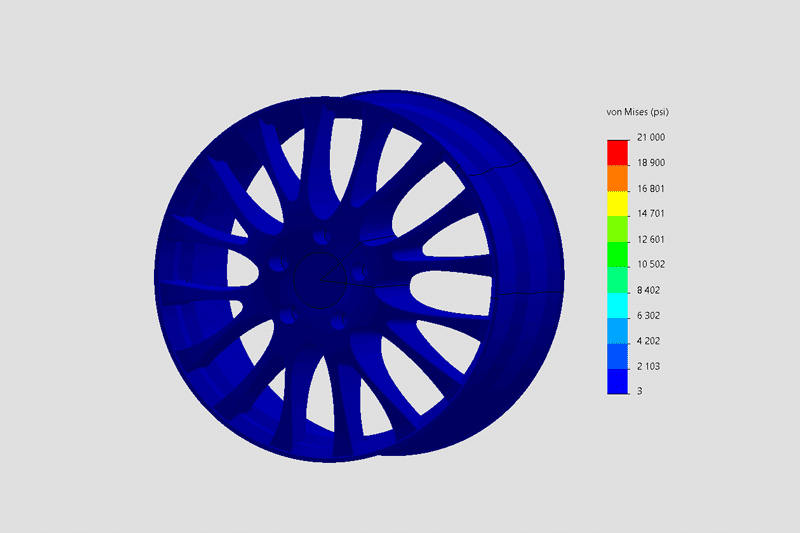
What other benefits can the Simulation service offer manufacturing and product development customers?
Yousef Imani: “In the development of your product, buckling, a phenomenon of elastic instability of a structure, can occur at any time. To escape a heavy load, it automatically generates a failure of the product such as a deformation which thus opposes less stiffness to the load. This is why we carry out analysis of structures subjected to compressive loads such as the connecting rods of an engine, the arm of a loader, the chassis of vehicles or even on the legs of the support of a tank.
We have other types of analysis which allow, for example, to know the reaction of your product in its dynamic behavior: modal analysis. You will be able to meet the standards of your sector. If you would like to check your product’s resistance to heat or cold and test its thermal durability, our thermal and thermo-structural analysis will help us make recommendations. If you want to evaluate the effects of fluids on your product, calculations on their movements will be necessary. The evaluation of fluid mechanics will be invaluable in meeting the technical requirements of your product.
The quality of a product is also based on its durability, its safety, its resistance to shock, drop, etc. Finite element analysis confirms the viability of product development concepts and is among the most essential steps for optimization.”
Expert advice
Yousef, why should a company use simulation in product development?
Reducing product development time and cost
Numerical simulation is well suited to reduce the number of prototypes manufactured and tested in the product development process; therefore, reducing the time and cost of product development. Thus, a single numerical model designed with specialized software can be analyzed in order to validate the behavior of the complete product, an assembly or a component under different loading cases. The specialist can more quickly determine the critical factors that can affect an entire structure, understand why failures can occur and correct the situation before it even occurs. In a very competitive market where time-to-market and cost are critical factors, numerical simulation offers many advantages.
Product optimization
By determining how a product will be used and in which environment it will evolve, simulation can help optimize its geometry, design and mass. It is also very useful for certain time-dependent problems such as in collision simulations in which the deformation of an area can spread to other parts of the structure. The quality and durability of a product can be optimized for its future use by using different analysis tools such as topology optimization, generative design or fatigue analysis.
Validation of concepts
Numerical simulation helps engineers detect any design issues in the early stages of product development. Therefore, they could modify or even replace their designs with those that are more efficient in terms of cost, strength, and performance. With the detailed visualizations, engineers can easily spot any vulnerabilities in the design and depending on the application of the final product, may be able to use the appropriate types of analysis to validate their initial designs and move forward in their product development process.
How does Merkur stand out from its competition?
- Merkur: 29 years of expertise and projects
- The relationship of trust with the customer: knowledge of his history, support, collaboration, versatility and good customer satisfaction. The objective: to exceed the client expectations
- The diversification of knowledge and global analysis: multidisciplinary team, knowledge of processes, design, and methods in product development
- Merkurian methodology in simulation: preparation, development of scenarios and follow-up (recommendation and modification of the design if necessary)
- Simplification of work or increasing efficiency
Learn, seek and accompany the client at all times"
Yousef Imani, P.Eng., Ph.D., Director of simulation projects – Merkur Inc.
Conclusion
Led by Yousef, the numerical simulation team (FEA) is at your disposal to analyze and simulate your product concepts. With a range of analysis and documentation of the results, our Merkur experts are able to present you with recommendations that will optimize your products, improve your performance and allow you to develop and obtain an optimal and innovative product. If you already have an FEA department but you lack resources or if you do not have the expertise in-house, we will be happy to support your requirements. Do not hesitate to contact our team!
The assistance provided by Merkur's numerical simulation team has been extremely valuable in meeting the needs of our customers in a time of high demand for our products. We especially appreciate their professionalism and dedication in carrying out the tasks we entrust to them."
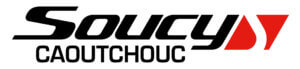
Magella Bédard
Department Manager, Numerical Simulation Soucy Caoutchouc
ABOUT US
MERKUR is a firm of experts in manufacturing performance and innovation and has been doing so for over 25 years. From strategy to execution, its sole objective is to make Quebec’s manufacturing companies more efficient by offering innovative solutions in product development, operational excellence, manufacturing engineering, automation and smart factory. Merkur is proud to contribute to innovation and productivity in Quebec!
KHROME PRODUIT TRANSPORT is a manufacturing integrator located in Drummondville specialized in the design and manufacturing of train car interiors and exteriors. Its strength comes from its great engineering capacity and its manufacturing agility. Among its customer portfolio, there are major manufacturers such as Alstom, Bombardier Transportation and Kawasaki Rail Car.
SYNKRO is a software developed by Merkur and designed specifically for high-performance manufacturers. It collects, classifies, and distributes the right data to the right people at the right time. SYNKRO gives you a real vision of your operations. SYNKRO is the software solution that finally connects your floor and your offices.