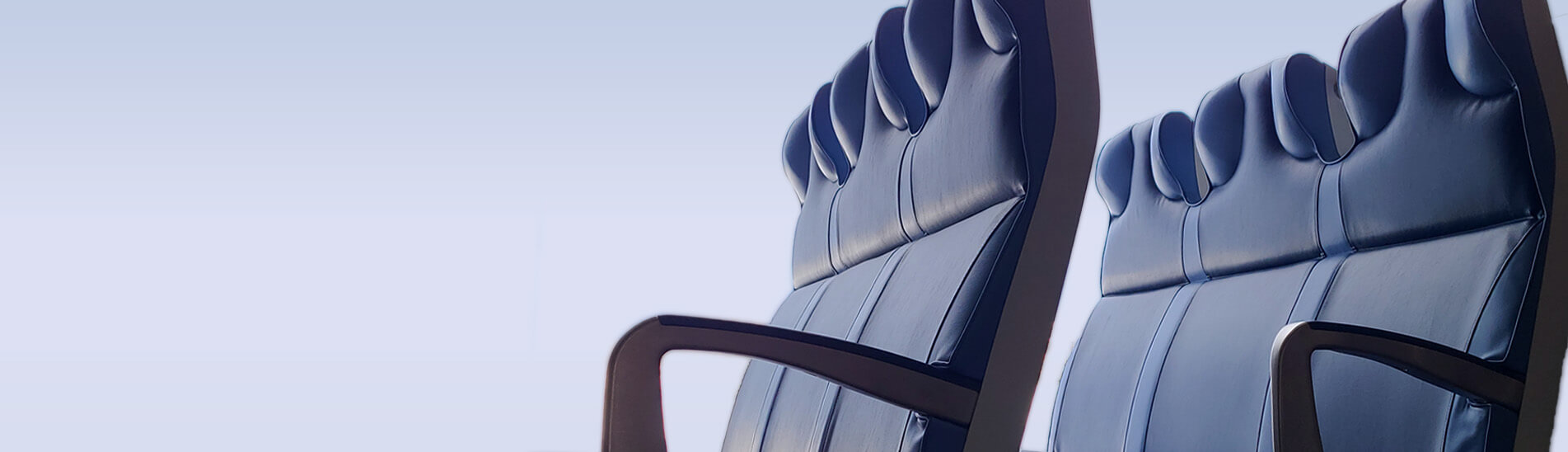
MANUFACTURING INDUSTRY
DESIGN AND SIMULATION FOR THE PASSENGER SEATS OF THE LONG ISLAND RAIL ROAD IN NEW YORK
Collaboration with Khrome Products-Transport for Kawasaki and Long Island Rail Road (LIRR)
Developed for the daily commuters on trains serving the eastern suburbs of New York City located on Long Island and the northern suburbs of Connecticut, the M9 seats were manufactured by our client, Khrome PT, on behalf of Kawasaki. The twofold objective was to comply with the safety standards and constraints imposed by the transportation authorities and to meet the technical specifications set by the car manufacturer, all within the established budget.
Merkur’s Mandate
Kawasaki entrusted the development and manufacturing of the new seats (M9) to our customer Khrome Products Transport (KPT). In this traditional and highly regulated sector, the weight of the seats had to be reduced by 25% without increasing production costs. Merkur was therefore entrusted with the design, the numerical simulation tests as well as the tests and validations in order to respect the specifications, the standards and safety constraints imposed by the transport authorities (APTA*) as well as the budgets set by Kawasaki.
*APTA : American Public Transportation Association.
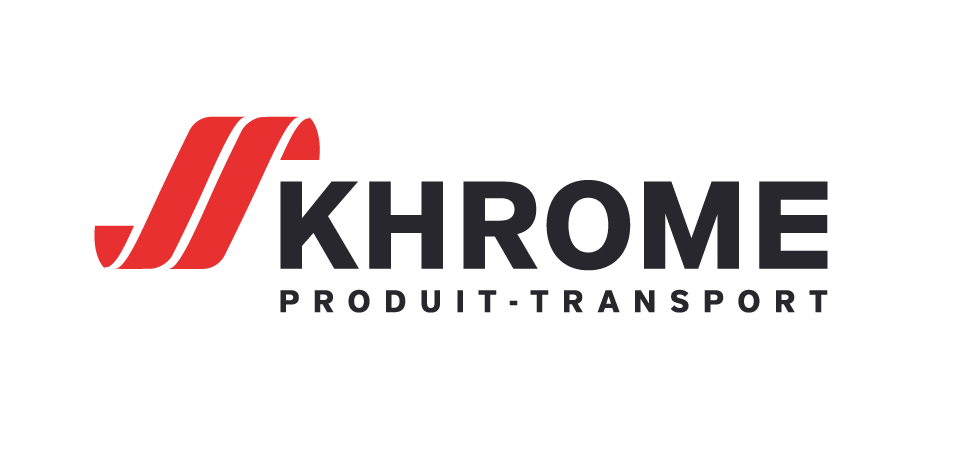
The Impact of Digital Simulation on Product Development
With expertise in design and digital simulation, Merkur’s team worked with Khrome PT’s team to produce the M9 seats, meeting the most stringent requirements of North American standards for reliability and safety (APTA). The technical specifications set by Kawasaki were also scrupulously respected in order to manufacture custom-made, resistant and durable seats.
The numerical simulation carried out beforehand made it possible to reduce the number of physical tests, which in itself represents a cost saving. Indeed, in this context, the numerical simulation quickly identified the stress concentration zones of the seats due to the different load cases. Beyond comfort, finish and resistance to vandalism, the recommendations made had an impact on the weight of the seats and their durability.
After the first iterations of simulations, modifications in the choice of materials were made in order to increase the strength of the seats in the high stress areas. Once these steps were completed, a first prototype was manufactured and then physically tested to validate the numerical models. Cycling tests were conducted in Khrome PT’s laboratory by our team of engineers while destructive tests were performed by a Canadian automotive research and testing center, also supervised by our engineers.
The M9 seats of the LIRR train are currently integrated in cars in service that are equipped with 41 seats each: they meet the current requirements of passenger car interiors where design and comfort prevail.
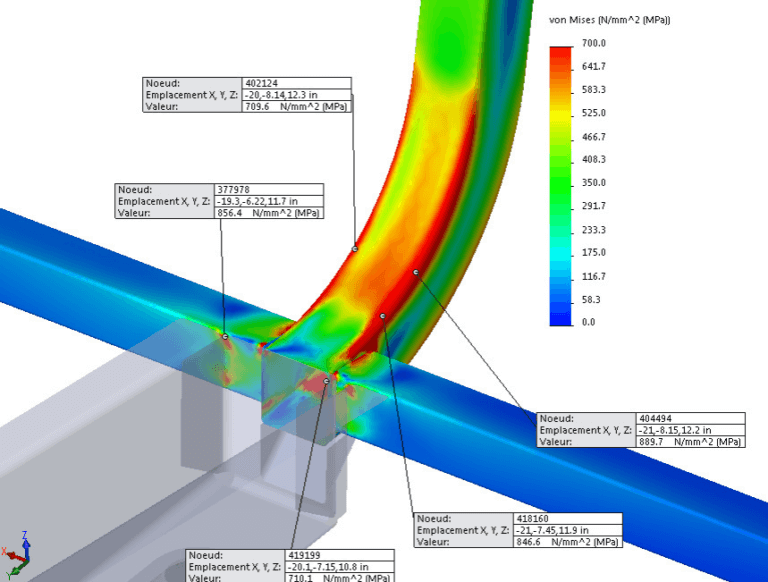
Results
- Compliance with safety standards and design criteria (APTA)
- Weight optimization of seats through design and numerical simulation expertise
- On-time delivery
Benefits of the Collaboration with Merkur
- Reduction in the number of physical tests thanks to upstream digital simulation
- Innovative solutions that meet performance and cost objectives
- Support from design to physical validation of train seats
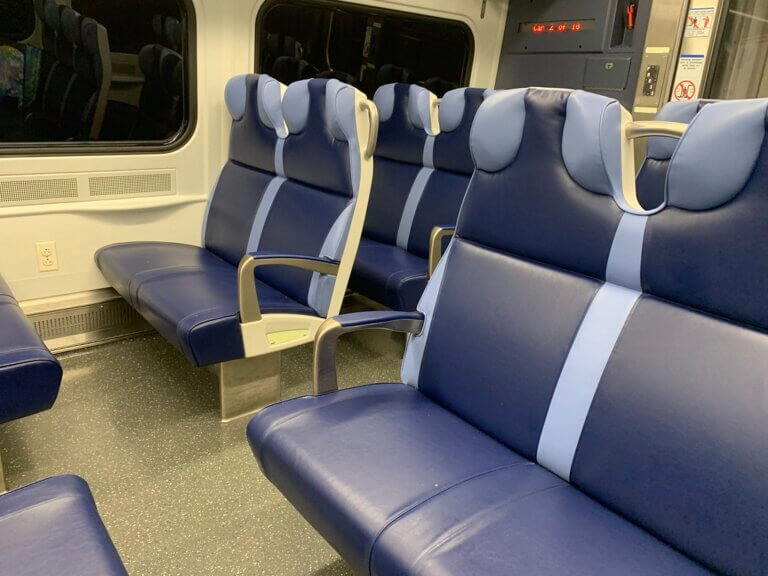
Merkur’s Key Expertise
- Complete product development expertise with a unique offering
- Flexibility, availability and trust
- Experienced team with a proven methodology
- Reduced product development time and workload