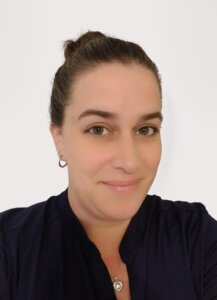
Sonia Villiard
Mechanical Project Manager
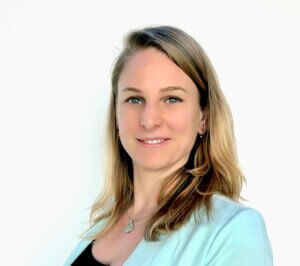
Elly Neyret
Ing. PRT manufacturing project consultant
If you want to train your new employees more quickly, or guarantee the quality of the tasks they perform, then designing effective work instructions is essential in a context where manpower is at stake.
Real support to production, quality work instructions will enable you to increase output, improve efficiency, and reduce product non-quality, despite the shortage of skilled workers.
Your main concern is to ensure the quality of your work instructions so that they are beneficial to your manufacturing business.
Quality instruction is an integral part of corporate culture. It must be kept up to date by qualified staff, adapted to its audience, have a sufficient level of detail, and be part of a reliable and functional process for distributing updates.
But how do you design these quality work instructions ?
Our Merkur experts have developed a methodology with many practical tips to help you achieve this.
Whether you want to maintain or update existing work instructions, or create new ones following an incident or a new standard, for example, follow these 4 key steps !
READ ALSO :
Why Write Quality Work Instructions?
Step 1: Validate the Balancing of your Production Line
Whether it’s a project to implement new work instructions, or to improve existing ones, the first step is to ensure that each workstation requires the same workload per operator throughout the line
Naturally, in a project to update or revise your instructions, this step will enable you to check the balance of your positions and operations and adjust them if necessary, whereas for an initial implementation, this definition will require a more in-depth analysis.
You’ll start with a complete study of your production line in its entirety, then go into detail and analyze each of your workstations by asking yourself certain questions: What is the customer’s takt time, what is the line’s cycle time, how many workstations are required and, finally, how to balance operations on these different workstations?
Asking yourself these questions will enable you to study the work instructions deployed for each type of workstation: How many instructions will you assign to each workstation? Which instructions will you associate with which workstation ?
Tip: Remember to include end-users !
Involving end-users right from the start of your analysis phase is essential.
Operators, supervisors, quality managers or safety coordinators will help you to simplify and highlight points of vigilance that you may not have seen.
Involving the right contacts will enable you to obtain the latest updated or recent information on SIREP standards, for example, in order to draw up your work instructions.
An operator involved in the preliminary study of the line and the workstations covered by the work instruction will feel more concerned by it, and this will facilitate change management.
Step 2: Define the Level of Detail
Once the overall analysis of your production tool has been carried out, the second step is to define the desired level of detail in your work instructions.
Are you going to write a general instruction for your entire workstation, covering all assembly and manufacturing options, or will you prefer an instruction by product type, operator or operation?
Adapt the level of detail to the purpose of your instruction: An instruction used to support training on the operation of a new model will be intentionally detailed. The same applies to operations with a major impact on the quality and safety of the product or operators. In such cases, precise instructions are essential.
For a standardized workstation, a more general instruction, presenting each step of the production process, will be more appropriate.
Note that an instruction may be temporary, to accompany the introduction of a new product, process or tool. Once the learning period for this new feature is over, it should be archived, so as not to add to the workstation’s documentation.
Step 3: Draft / Approve / Distribute Work Instructions
Now that your production line is balanced and the level of detail of your instructions is defined, you can enter the writing phase.
Keep in mind everything we’ve discussed above, i.e. maintaining a standard and including comments and restrictions received from end-users and/or quality and safety managers, while respecting the balance and precision defined beforehand.
In a prototyping phase, we recommend that you first share your work instructions on paper. This will enable operational staff to note any comments or corrections they need to make to reflect the reality of the floor.
Following this step, go through a quality check to validate that the process described complies with the required standards. Finally, it’s time to complete your standard media (whether paper or digital).
Tip: no matter who the writer is, your content must meet a certain standard.
Once you’ve completed your first draft, don’t neglect the process of validating your instruction. This involves several stages: verification, approval and distribution. Operational, quality and product engineering teams will be able to ensure that the work instruction meets the quality standards.
Step 4: Ensuring the Correct Use and Updating of your Work Instructions
At last, your work instruction is approved and validated! Congratulations on your success!
Now you have to make sure it’s applied, that it lives and that it’s in a perpetual updating process. An obsolete instruction forgotten in a corner of your workshop is worthless. So make sure you use it properly and keep it up to date.
Suggestions from line operators should be passed on. Feedback from the floor will show whether your instruction is too detailed or, on the contrary, too light.
Tip: Make sure you’re open to suggestions and comments.
It’s important to encourage feedback from the floor, but it’s even better if the documentation department pays attention. Instilling open communication within your company encourages constructive feedback.
The notion of transparency is crucial in the process of distributing and communicating your instruction. Indeed, if certain modifications cannot be implemented, it is important to come back to your team to explain that this suggestion has been studied, but that it is not possible to implement it. For example, it may be incompatible with the level of quality or safety required or imposed.
CONCLUSION
In conclusion, there are several points to bear in mind when designing effective work instructions :
- A corporate culture is essential, as is a methodology and a trained, committed team.
- A work instruction must stand the test of time.
- Involving your teams from the outset ensures that end-users are committed to respecting and applying instructions, and encourages feedback.
- Transparent, open communication is the key to quality work instruction.
You now have all the keys you need to boost your productivity and the training of your new employees with quality work instructions.
If you need support, Merkur can help you analyze your needs, deploy a global continuous improvement process, define methods, draw up and implement work instructions, and even train your teams. Contact our experts.