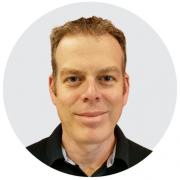
Francis Gendron,
Expert in mechanical design and motorization
Francis is a mechanical engineering technician trained at Cégep de Sherbrooke, and has nearly 30 years’ experience in product development for multiple vehicle systems, as well as in the design of tooling and jigs for different manufacturing processes, giving him a wide range of knowledge in the field of mechanical engineering.
In the complex world of product design, certain approaches stand out, such as DFMA (Design for Manufacturing and Assembly), which enables products to be designed in such a way as to make them easier and less costly to produce and assemble. When integrated with simultaneous engineering, DFMA brings many advantages, which we will explore in this article.
READ ALSO: 3 Bring your products to market successfully with the product development process
DFMA in simultaneous engineering
Simultaneous engineering is an approach to design and development in which all teams work in parallel on the project, rather than sequentially. DFMA’s activities fit perfectly into the ideology of this approach; they enable product design to be optimized with the manufacturing teams, avoiding costly backtracking and ensuring that the product will be well-designed, cost-effective and easy to assemble, maintain and recycle.
The DFMA offers many advantages, including:
- Optimizing manufacturing processes: by simplifying or eliminating parts or assemblies, DFMA improves overall production efficiency by reducing the number of manufacturing and assembly operations, and thus has a direct impact on costs and lead times.
- Modularization and standardization: product design using standardized modules or sub-assemblies reduces the number of unique parts and facilitates product assembly, maintenance and repair, also reducing costs and lead times.
- Quality improvement: well-thought-out design for manufacturing and assembly reduces manufacturing errors, resulting in higher quality end products.
- Shorter development times: by integrating DFMA early in the design process, development times can be reduced as potential manufacturing and assembly problems are identified and resolved earlier.
- Facilitating innovation: finally, by simplifying manufacturing and assembly processes, DFMA frees up resources and time that can be reinvested in innovation and continuous product improvement.
HOW TO for an effective DFMA
Many would be tempted to believe that integrating DFMA into the product development process adds a certain amount of complexity, but the various people involved in the project quickly realize the time saved and the significant gain in profitability at the end of the day. For the most efficient integration of DFMA, here are the main steps to follow:
- Analyze product functionalities and requirements: it is imperative to assess and understand from the outset what the part will be used for and what its precise needs are.
- Evaluate the product design and manufacturing process: at this stage, we need to decide on the means of manufacturing, the manufacturing capability of our company and our suppliers, and the different materials possible without altering the quality of the part, in order to establish all the possibilities, evaluate them and make an informed choice.
- Implement the chosen solutions and ensure that they meet initial expectations.
Successful integration of the DFMA
At Merkur, several mandates have been successfully completed thanks to the integration of DFMA into the product development process.
For example, for one of our customers, the integration of DFMA enabled the reuse of mechanical propulsion elements from an existing vehicle, as well as the cab of another truck, in the development of a new product. This approach led to a significant reduction in development costs and a much shorter time-to-market.
Similarly, for another customer, the DFMA highlighted a dimensional problem in the development of a new vehicle. This problem could have doubled shipping costs. Thanks to the early identification of this problem, corrections could be made quickly, avoiding not only delays but also considerable additional costs for manufacturing tooling.
In this way, the application of the DFMA has not only optimized costs and deadlines, but also ensured the quality and efficiency of development projects.
How Merkur supports you in integrating DFMA in simultaneous engineering
Merkur supports its customers in the integration of DFMA by providing strategic advice, specialized teams and a personalized approach tailored to the specific needs of each project. DFMA is in our teams’ DNA and part of our toolbox: contact us today to get your product development project off to a good start!