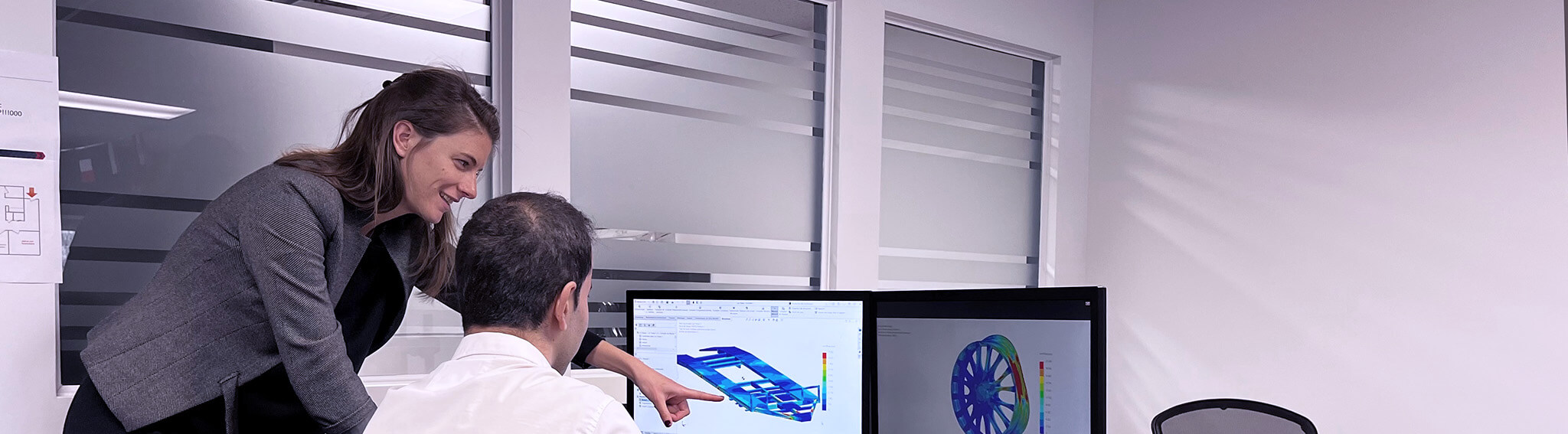
NUMERICAL SIMULATION (FEA)
Product Optimization, Product Development Time and Cost Savings
Our experts at Merkur are there to support your product development projects by validating different concepts using analytical calculations, prototypes, and test benches. Merkur has a FEA (Finite Element Analysis) team that is committed to working with your team to analyze and simulate your product and tooling concepts. Merkur also helps you to optimize your processes, run tests, document results, and make required recommendations, in order to allow you to obtain a quality product and to stay ahead of the competition.
Simulation & Validation
You leave nothing to chance nor does Merkur!
We excel at analysis and simulation because we know that this step is essential for you in the development of your products. This allows us to ensure an optimized product design while helping you to reduce the duration and costs of validation. We specialize in finite element analysis, product performance, Design of Experiment (DoE), and statistical/dynamic studies as well as in the collection and processing of experimental data.
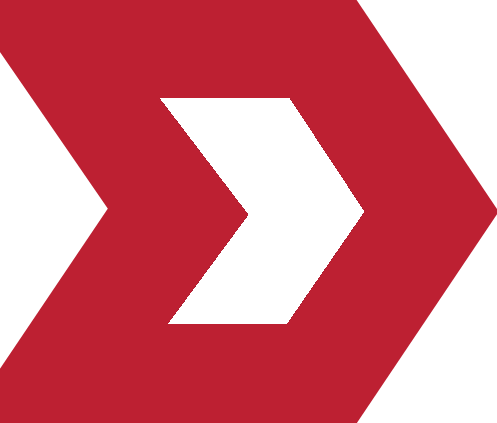
Static & Dynamic Analysis
Is your product sufficiently resistant to different loads throughout its life cycle?
Our FEA experts support you and determine your product development issues such as: reaction forces, safety factors and possible deformations. Merkur collaborates with you by doing all the necessary analyses whether static or dynamic, linear or non-linear. Regardless of your sector of activity (automotive, aeronautics, etc.), our experts will be able to help you.
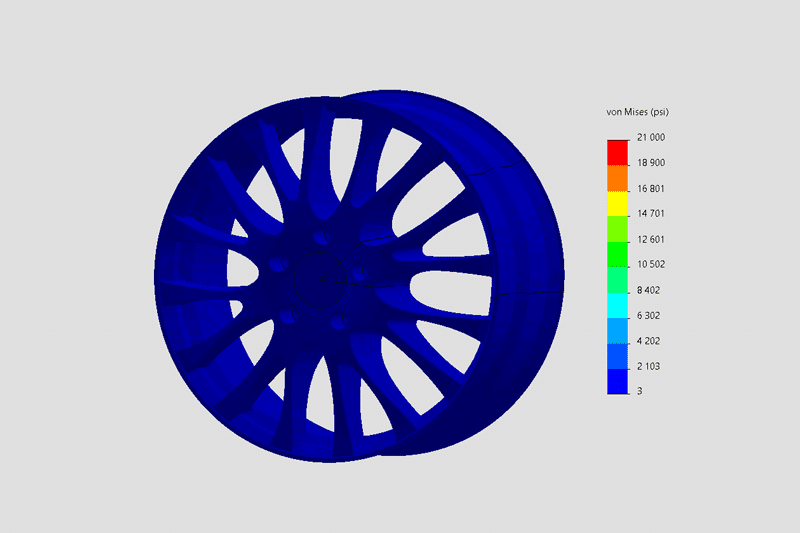
Static analysis of a rim
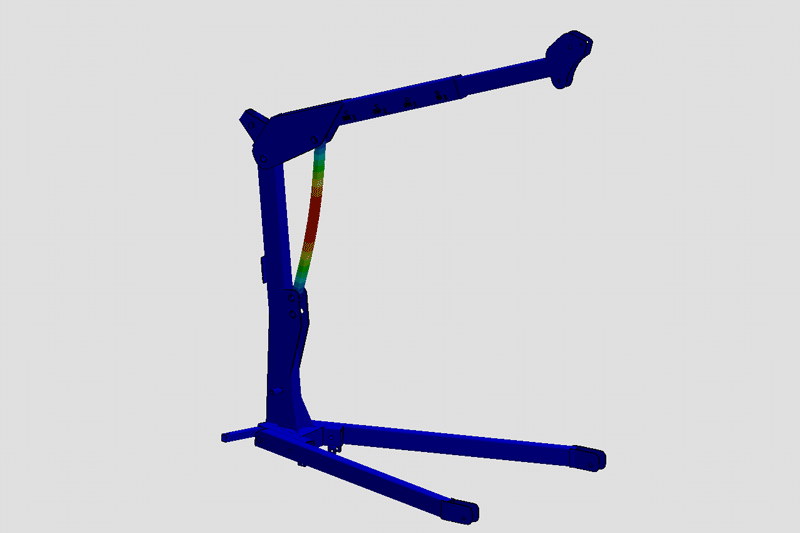
Buckling analysis of a lifting crane
Buckling
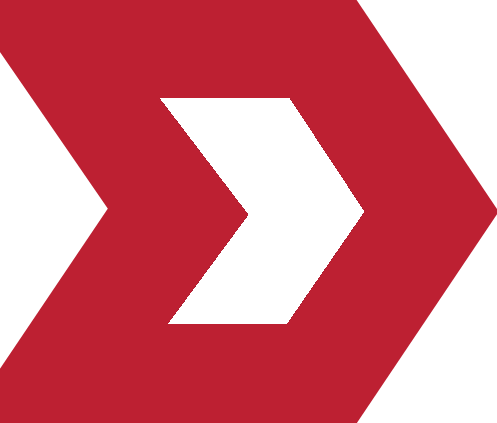
Are your products stable enough not to buckle?
In the development of your product, buckling can occur at any time, even under minor loads. Analyzing structures subjected to compression loading such as engine connecting rods, loader arm, or tank support legs is essential, because buckling can cause your product to fail. This is why we carry out this type of structural analysis.
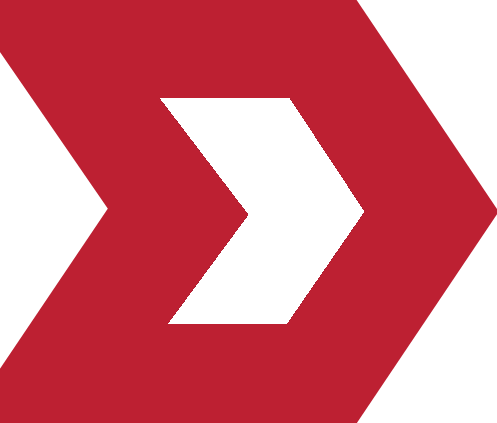
Modal Analysis
How does your product react under dynamic loads?
This vibration-based analysis helps extract the dynamic behavior of your product structure (natural frequencies, mode shapes, damping ratios, etc.). Our team will allow you to validate your products through a modal analysis to ensure that it meets the standards and expectations required of the sector.
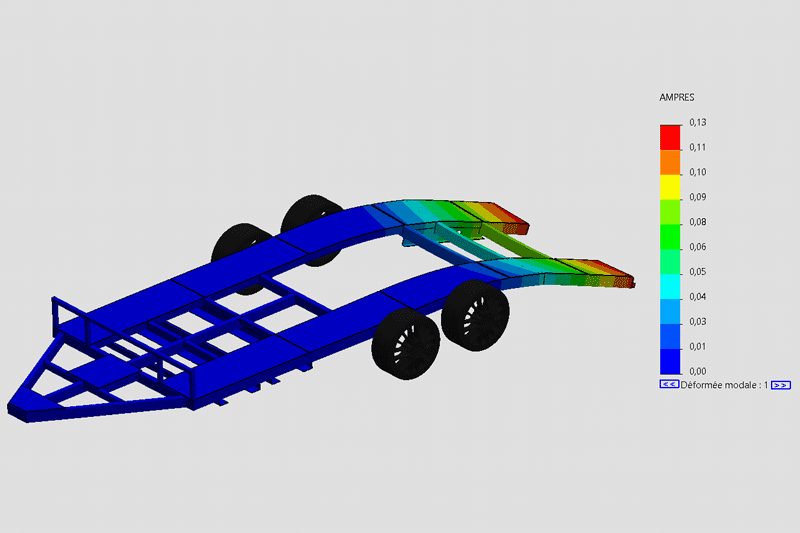
Modal analysis of an aluminum car trailer structure
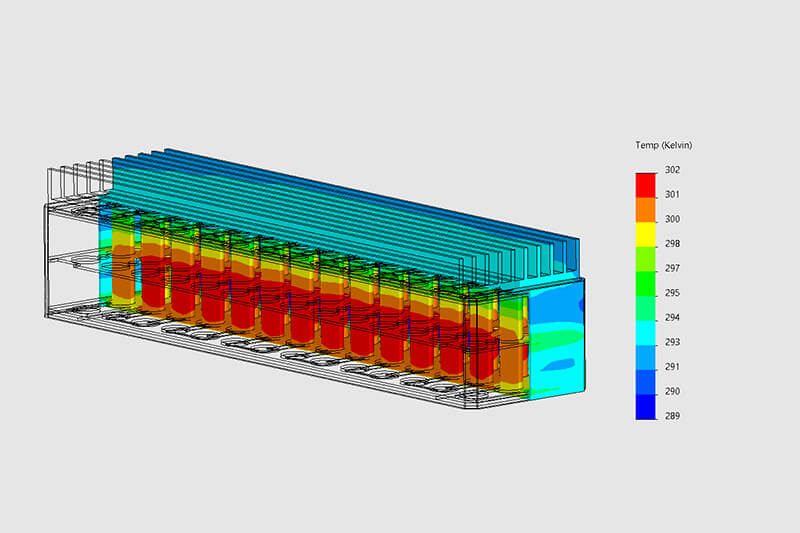
Thermal analysis of an e-bike battery pack
Thermal and Thermo-structural
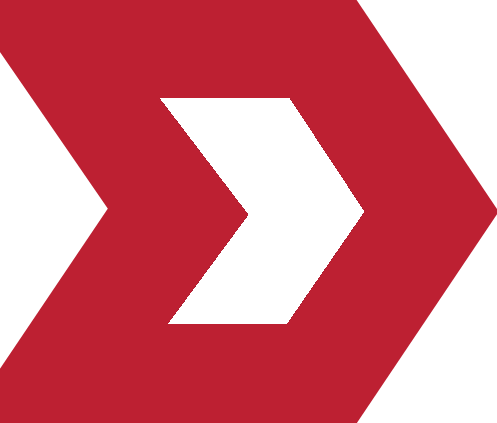
Do you want to make sure your product is resistant to the impact of heat?
Our experts can address your concerns regarding: impact of temperature on a specific model, product cooling, possible failure, etc. Thermal analysis of your products (electronic devices, electric motors, battery packs or HVAC) ensures thermal durability, quality, and performance. Our team can provide direction for optimization of your products.
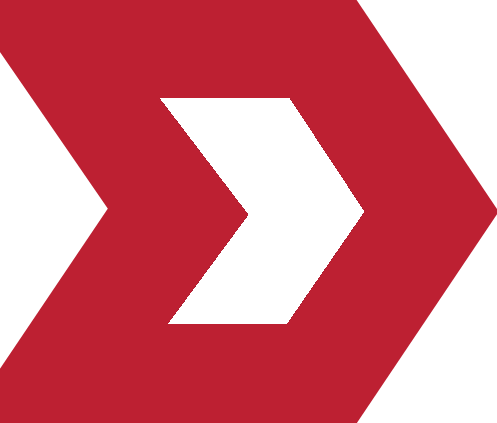
Fatigue & Fracture
Are you worried about the longevity and quality of your product over time?
Just like you, we understand that your product must demonstrate excellent quality, flawless durability, extended life, as well as be reliable in terms of safety. Studying the resistance of parts and cracks is essential to validate the quality and fatigue stress of your product.
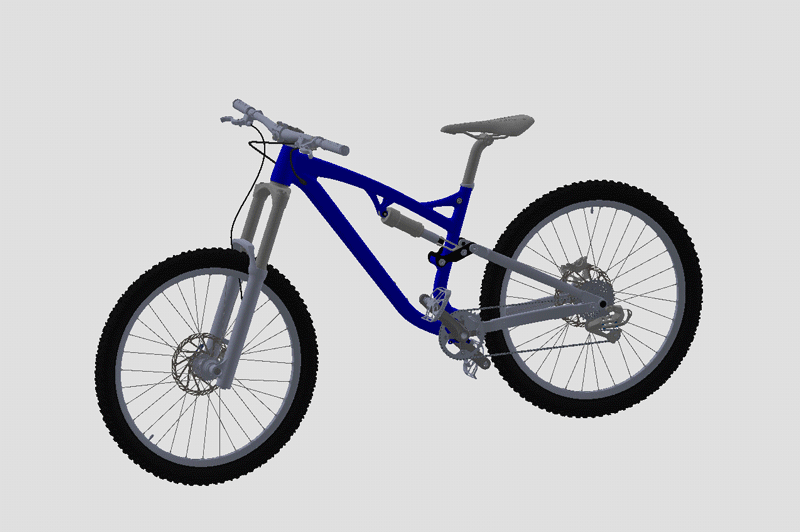
Fatigue analysis of a mountain bike frame
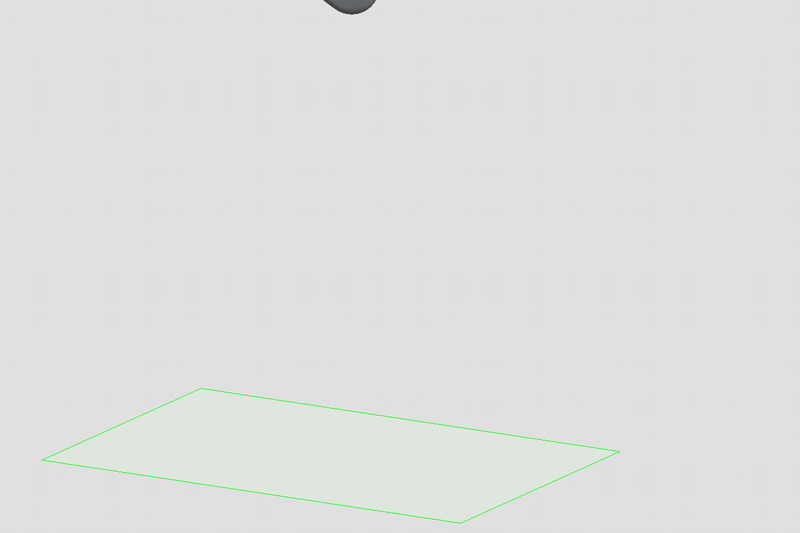
Drop analysis of a cell phone
Drop Test Analysis
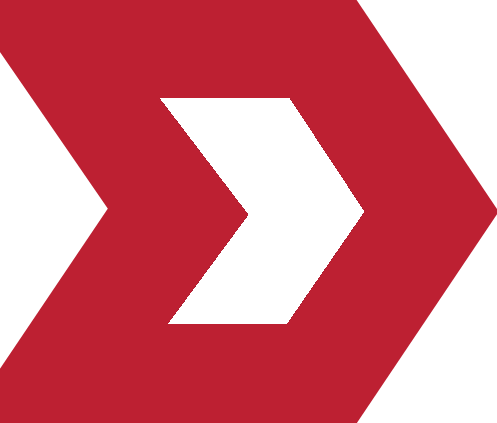
Can your products undergo impact or drop loads?
Our FEA experts are there to help you determine the risk of impact or drop to ensure that your products will withstand these types of situations. In order to provide better performance in the event of an impact, we will give you recommendations on your product design based on drop and impact analyses.
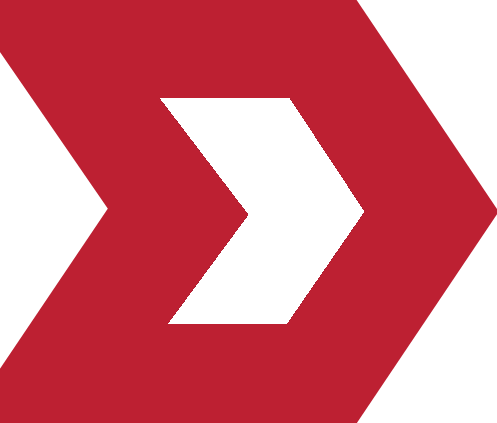
Topology Optimisation & Generative Design
More than ever, today’s market requires lighter and aesthetically refined products.
Our team of FEA experts understands this and helps you optimize your concept for the most suitable geometric shape while maintaining an acceptable level of stress and a lighter total mass. Another positive aspect of topology optimization is that an optimized part requires less material in production. With optimized models and by promoting 3D printing, t wasted material can be reduced.
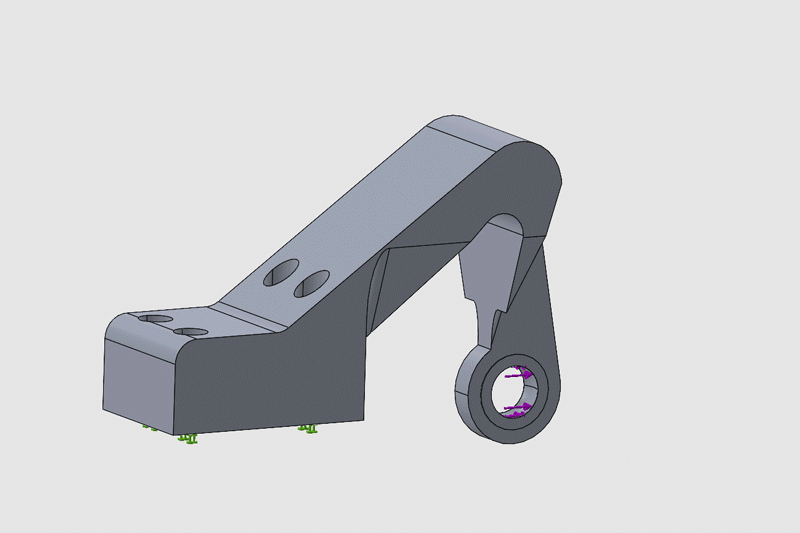
Topology optimisation of a support bracket
The assistance provided by Merkur's numerical simulation team has been extremely valuable in meeting the needs of our customers in a time of high demand for our products. We especially appreciate their professionalism and dedication in carrying out the tasks we entrust to them."
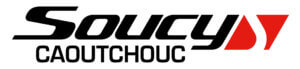
Magella Bédard
Department Manager, Numerical Simulation
Soucy Caoutchouc