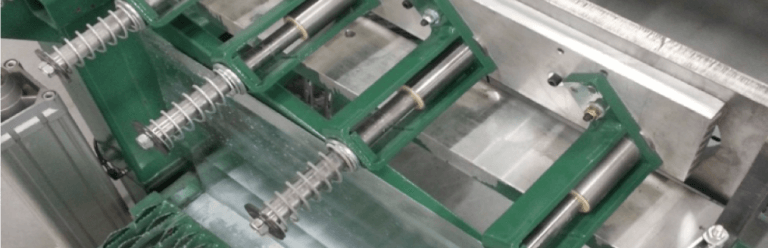
MANUFACTURING INDUSTRY
Optimisation of a new plant’s secondary operation lines
A transportation products manufacturer with a global presence wanted to start manufacturing large composite parts in a new plant.
The challenge? Design 24 workstations in a new one-piece flow assembly strategy. Through the development of advanced and automated tooling, the company benefited from reduced set-up times and improved overall operational performance.
Actions needed to be taken to meet this challenge
Merkur specifically contributed to the optimisation of this new secondary operation line by carrying out the following tasks:
- Modernised tooling and integrated automated elements
- Added an auditable and repeatable high-quality level
- Reduced reject rates from 10% to 0.07%
- Developed more autonomous and versatile tooling to reduce cycle times
- Reduced the number of operators per cycle time
- Designed inspection and validation templates
- Supported the implementation and start-up of new installations.
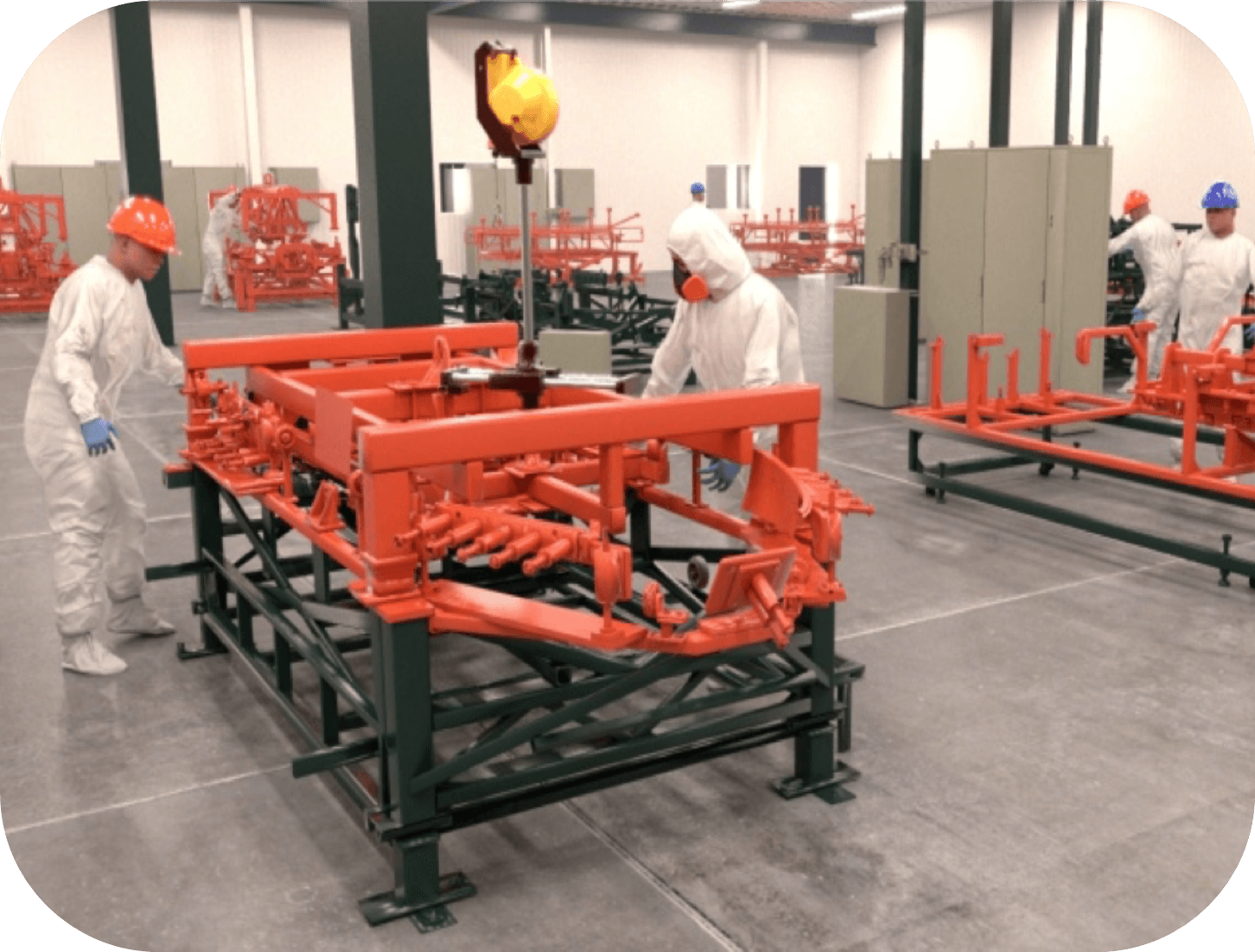
24
Different versatile jigs
15
DIFFERENT PART MODELS
REDUCTION OF FAILURE RATES FROM
10 to 0.07 %
More specifically, design 80 different versatile templates to optimise and ensure the mixed production of approximately 15 different models of parts in unitary flow, many of which will have up to 150 holes, not to mention the multiple cut-outs and characteristics specific to each model.
The multidisciplinary approach that does not leave manufacturers indifferent!
Merkur’s approach is to always offer the best customised solution to meet our customer’s challenges. Merkur has brought together its experts in tooling design, manufacturing engineering and operational excellence to precisely develop advanced, automated tooling that reduces set-up times, avoids human error, and improves the overall performance of our customer’s operations.