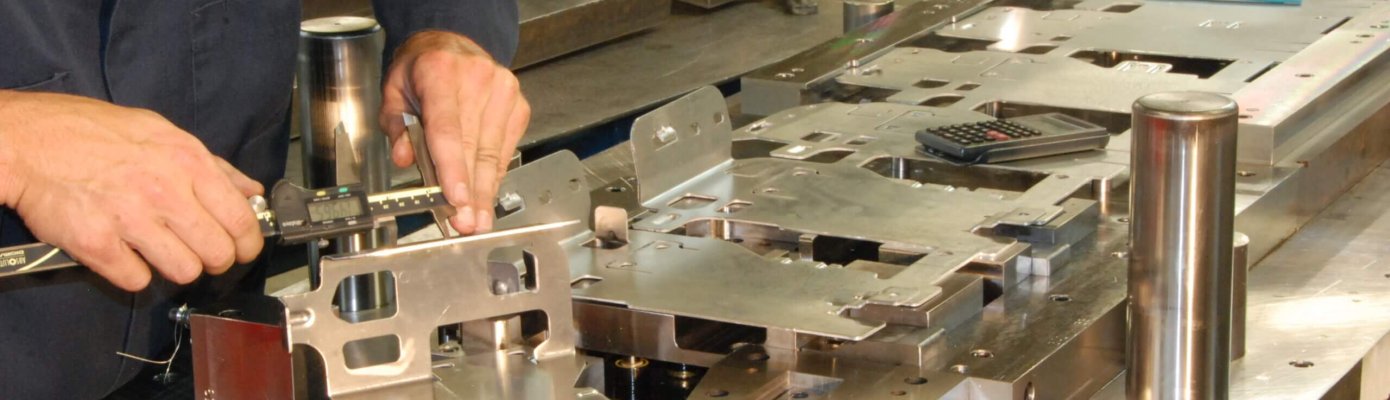
Manufacturing Industry
Matritech: A Large-Scale 4.0 Turnaround
Our client, Matritech, is a manufacturer of metal components with a varied production volume. Operating as a one-stop-shop, the company, located in Drummondville, combines different manufacturing processes: cutting, bending, stamping, welding, machining and assembling. With regular investments in new equipment, Matritech is at the forefront of meeting the manufacturing needs of its customers. Merkur has been supporting the Matritech team since 2019 in its important 4.0 shift. Let’s find out more about the successful strategy deployed in their company!
Digital Strategy and Operational Excellence: A Winning Combination!
It is in 2019 that Merkur begun its support process with the Matritech team. The most interesting digital opportunities for Matritech were first identified and then deployed, notably in the field of the smart factory and machine data acquisition and exploitation.
OBJECTIVE
Improve the performance of all plant operations by deploying a scalable technology solution. Use this “real-time” virtual manager to assist the production team in its daily operations and, above all, to gain in efficiency and productivity.
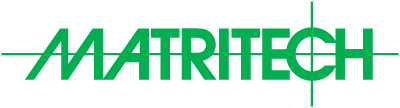
The preferred strategy at Matritech was the use of the small project approach.
This approach allows for rapid gains while making a smooth organizational change. This approach is all the more interesting since it allowed the Matritech technical team to appropriate the necessary knowledge for the maintenance and growth of the system. To update this strategy, Merkur accompanied the Matritech team in the realization of a review of the value chain in order to determine the neuralgic points and to extract a technological and operational strategy in order to establish a prioritization of the actions to be realized.
The implementation of the SYNKRO platform first made it possible to link the machine data with the information contained in the company’s ERP: the first performance indicators relevant to operators, supervisors and management have been established. Today, a global vision on the state of production is obtained in real time with more than thirty machines connected and coupled with information from the ERP. The versatility of Matritech’s operations implies a diversity of equipment on the floor to be connected ranging from bending machines, to stamping machines, to laser cutting and welding robots. The use of a platform like SYNKRO allows to support this diversity and to take advantage of all the information contained in these machines.
This first milestone allowed the implementation of the roadmap system supported by SYNKRO. This roadmap presents the prioritization of the forklift operator’s tasks to optimize his movements and avoid errors in the routing of the material to the different machines. This is an important gain, both for the operators and the forklift operator, who can thus concentrate on their respective tasks.
VIDEO YOU TUBE (FRENCH VERSION ONLY)
Real Gains and Numbers that Pay Off
The Merkur experts have implemented the SYNKRO software, which collects, processes and distributes digital data from the production floor in real time.
The Merkur approach: a partnership that makes all the difference.
Soon, SYNKRO will help Matritech achieve an even greater level of coordination, by creating the operator’s own tasks based on the end-of-production forecasts on each machine. By achieving a level of intelligent coordination between machines and humans, Matritech will be among those pioneers who dare to implement new ways of doing things in the industry!
Constantly evolving in its smart factory projects, the Matritech and Merkur teams form a lasting partnership where SYNKRO plays the role of a cornerstone in achieving Matritech’s strategic objectives.