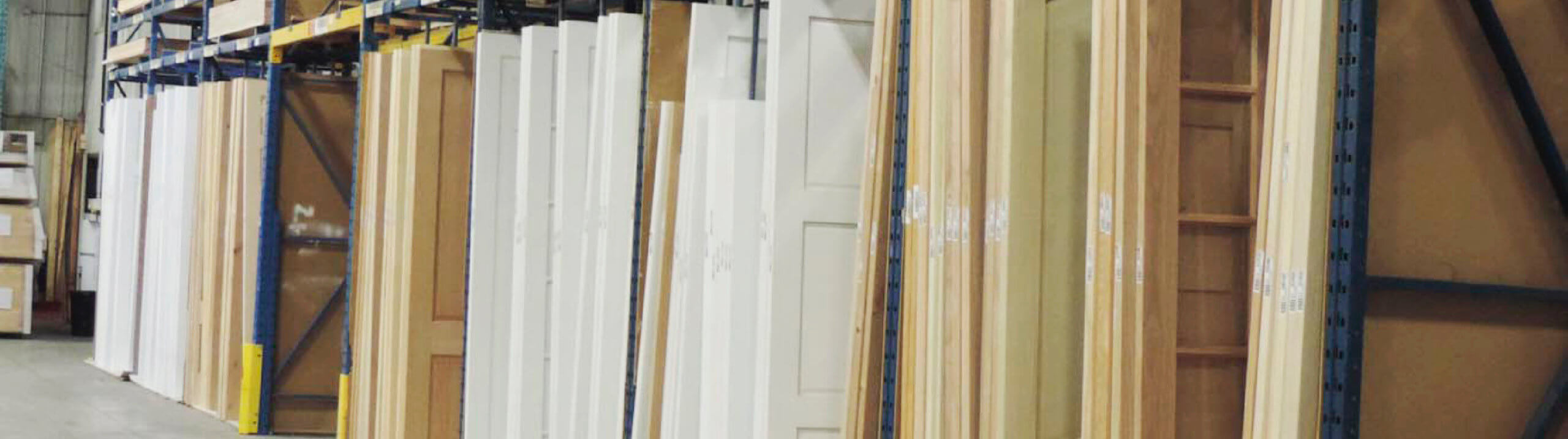
Manufacturing industry
Masonite doubles its factory production capacity and reduces delivery time by 30%.
Lemieux Doors (now the property of Masonite) specializes in the manufacture of wooden doors. After many years of strong growth, the company found itself dealing with a new industry trend: customization.
Faced with the challenge of achieving profitable mass customization, Masonite set out to increase the door maker’s agility and production capacity without compromising product quality or delivery time. With the support of Merkur’s experts, the company achieved its goal while maintaining high profitability.
Description of actions taken to address the challenge.
The challenge facing Lemieux Doors was a big one. To overcome it, we set out to boost its agility by overhauling manufacturing processes and procedures. Integration of new technologies and a factory makeover also helped the company achieve efficient mass customization.
In concrete terms, Merkur’s objectives for the project were to:
- Double weekly production using automated equipment
- Optimize production flows
- Reduce delivery times by optimizing the supply chain
- Achieve mass customization at a very competitive cost
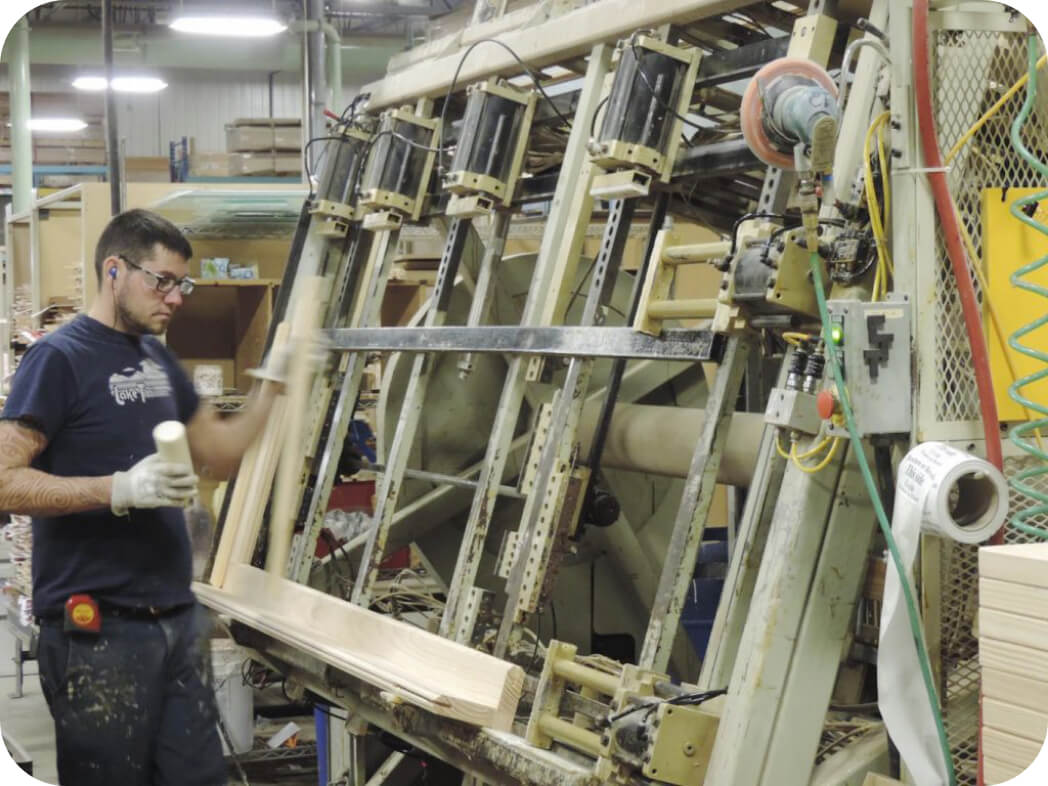
0 ft2
added to the factory floor
30%
reduction in delivery time
100%
increase in production capacity
The multidisciplinary approach that gets powerful results for manufacturers.
At Merkur, our approach is to always offer the best tailor-made solution for our clients’ challenges and needs. To boost Lemieux Doors’ productivity, agility, profitability, and capacity, we assembled a team of experts in manufacturing performance and manufacturing project engineering who did just that. Once again, this recipe proved to be a success.