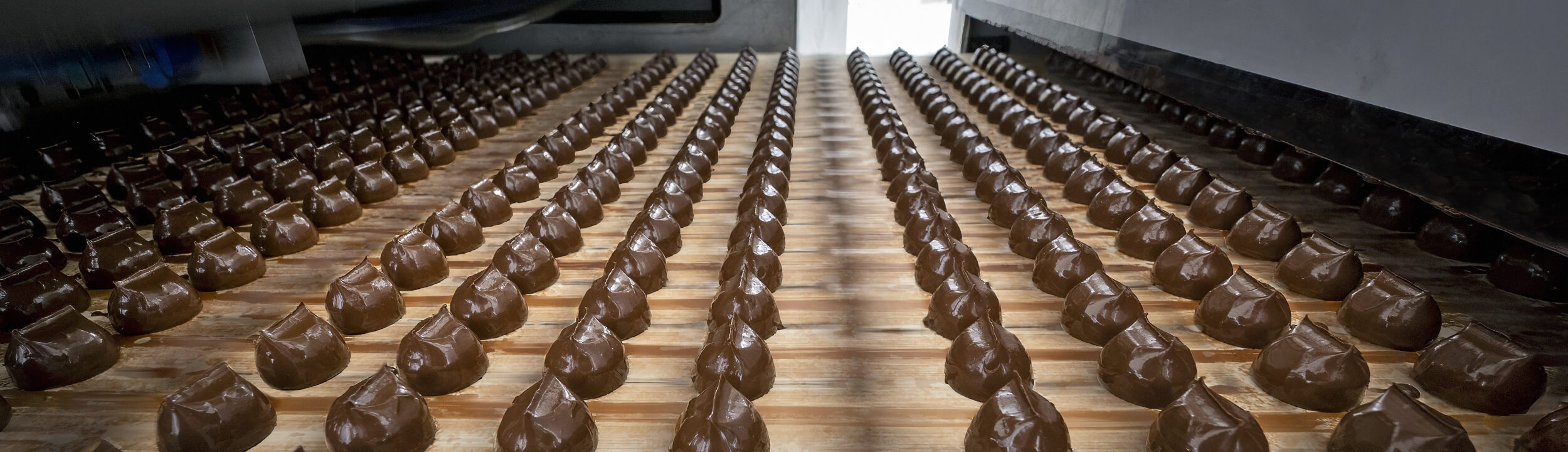
MANUFACTURING INDUSTRY
MANUFACTURING STRATEGY FOR CHOCMOD
Production Optimization
Collaboration with Chocmod’s Management Team
World leader in the industrial manufacturing of traditional French truffles, Chocmod distributes a wide range of chocolate products (chocolate truffles, organic truffles, chocolate-covered marshmallows, chocolate chips and bars) throughout the world. With a 3,000 m2 factory located in Saint-Jean-sur-Richelieu facing strong growth and an increasing demand from the United States, which constitutes 90% of its target market, a production optimization is necessary.
Merkur’s Mandate
Some of the plant’s equipment, designed and manufactured in Europe, has been able to produce a wide range of Chocmod products for some years in Canada. However, with the company’s significant growth, operational efficiency must be reinforced to respond to new market opportunities. The plant has about 40 permanent employees, and during certain periods of the year, the team expands to ensure increased production. In the context of a labour shortage, it is not uncommon for members of the regular team to have to fill certain gaps.
The Merkur team was therefore contacted to:
- Increase profitability
- Assist in production strategy
- Support management in its strategic investment planning for the challenges of the coming years
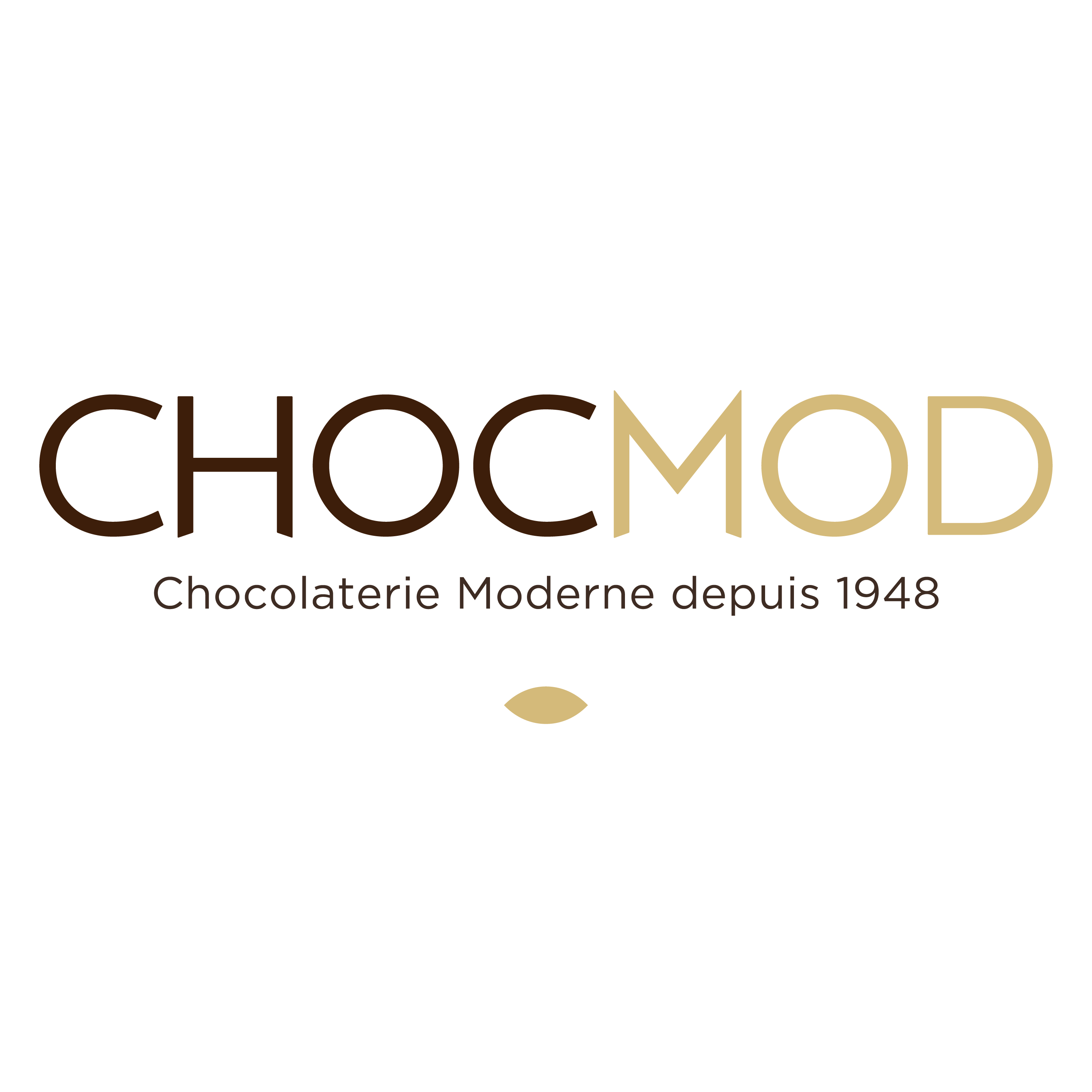
Objective
After a detailed analysis of the situation, a diagnosis is made by the Merkur team concerning the installations, the equipment, the workforce in place and the strategy to adopt. In order to meet specific needs (cold storage in particular), workspaces must be freed up in order to organize a reorganization of the plant. The production will have to focus only on cocoa-based products, the DNA of the Chocmod brand, while some products will be rethought for the future (nougat). This will allow Chocmod to consolidate the decisions taken regarding investors (space, maintenance costs and turnover forecasts with prospects).
The objective is to simplify the production process by standardizing tasks in work organization:
- Redefinition of team members’ roles
- Reduction of production time (operation maximization of the supply chain)
- Maximization of the machines (avoid machine stops).
Support is also provided on the production line since the roles of each person are redefined. This makes it possible to optimize the potential of each person in his or her work environment. With the optimization of workspaces, the reliability of equipment and technical levers, it is easier to support management in its strategic investment planning and to project the plant with a three-year vision.
A new recruitment perspective will also strengthen the production schedule.
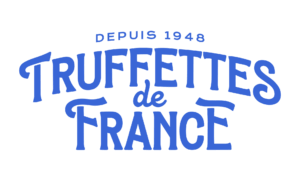
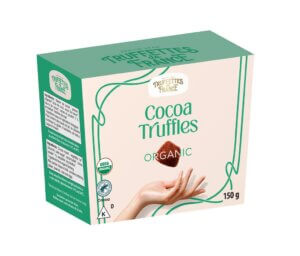
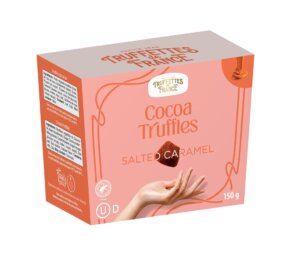
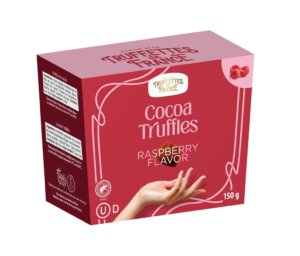
Outcome
- Optimization of time, workload, space, and equipment
- Consolidation of the company's strategic planning and documented decision support for a reduction of the product range: support in determining the company’s investment priorities and reinforcing the consultation with a detailed analysis (with the help of cross-referenced data)
- Obtain a continuous flow manufacturing with internal reintegration of certain outsourced activities
- Enhancement of the strengths and potential of the company
Benefits of the Collaboration with Merkur
- Limitation of the risks linked to the production with an optimization of the resources in place
- Production planning on an annualized vs. seasonal schedule (which creates more tension)
- Better planning of orders (raw material and packaging)
- Greater autonomy with regard to suppliers thanks to the internal reintegration of certain outsourced activities, for greater respect of delivery times
Merkur’s Key Expertise
- Complete expertise in continuous improvement (Lean manufacturing), work organization: all daily incidents have an impact on profitability
- Climate of confidence: ability to project oneself by identifying the challenges of the equipment (interviews, analysis, projection, and experience).
- Experienced team with a proven methodology that focused on valuing the company for optimal positioning in its market and its growth potential
- Innovation: help the company by proposing a technical solution to meet the needs (on the long term): automation of low added value activities
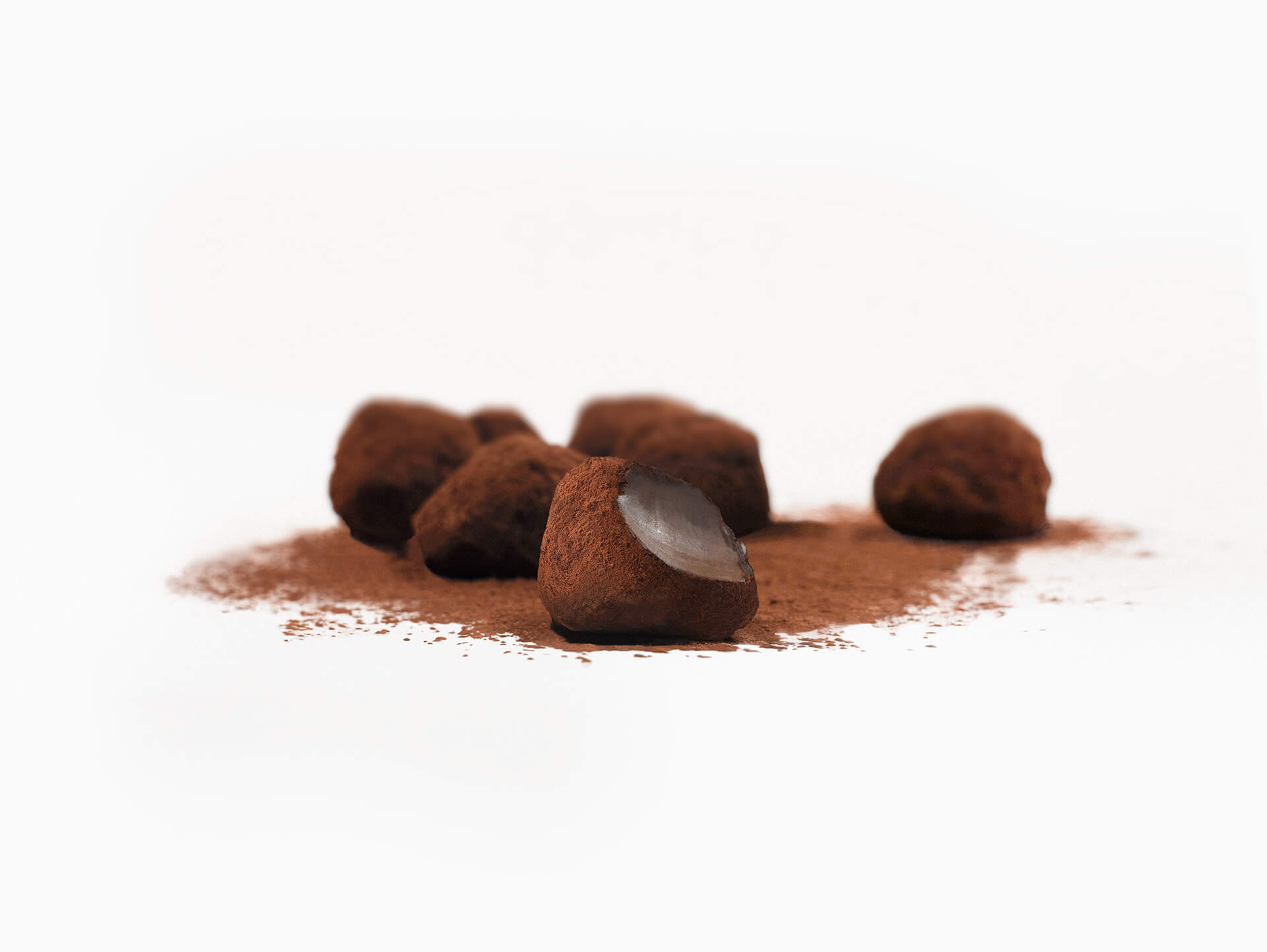