Measuring overall productivity can be both the most important and most complicated part of any manufacturing business and its facilities. There are many factors and many metrics principles to follow. Not being able to optimize and accommodate any one can result as a disaster for any manufacturing business. These following are some of the most important manufacturing key performance indicators to keep track of by any company.
1. Delivery Lead Time
Customer lead time represents the measured time between an initial order request and the delivery of a good to the customer. This information is a key in maintaining good relations with client, and keeping acceptable stock level. Try to keep this time to a minimum, and most of all, be as consistent as possible.
2. Overall Equipment Effectiveness (OEE)
Overall equipment effectiveness, or OEE, is a comprehensive measurement of how efficient your production lines and machinery currently are. Typically expressed in a percentage, as with most measures of effectiveness, this indicator is among the most commonly observed, as it is directly related to cost efficiency in the manufacturing realm.
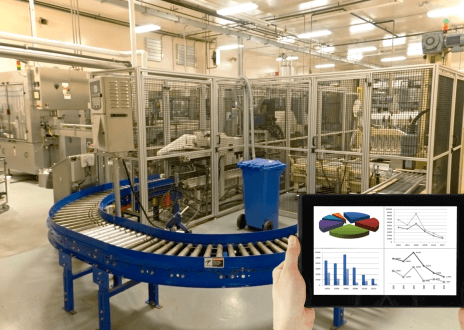
3. Throughput Yield
Throughput Yield indicates how often a product is exclude of the assembly line with one defects or more. This is a simple concept; when an item’s production has a rate of 95%, this significates that 95% of all produced items will be completed without any manufacturing default.
4. Labor Productivity
Labor Productivity is a significant measurement especially in facilities with large number of workers, as it statistically determine global facility’s efficiency. The total amount of produced items by facility is divided by the total number working hours worked in a specific time frame, giving an accurate measure of how much profit is currently made per worker.
5. Inventory Turnover
Inventory turnover rates are based on how many units a business sells and how quickly these units were sold. Keeping low stocks inventory is important, and not over-producing certain items.
6. On Time Delivery
Characterizing on-time delivery is critical to your delivery systems efficiency, and to maintain good relations with clients. Customers do not want late or unexpected shipments, and almost always value reliability over cost.
7. First Pass Yield
First Pass Yield measures how often items are produced correctly one the first time, thus do not require any corrective action. This is key in fast-paced and quality-sensitive facilities where remaking or correcting the same product can be time and cost-expensive.
8. Rejection rate
This ratio measures raw cost-effectiveness of your business where initial raw materials volume is compared to present raw materials volume in finish products. Maintaining this ratio to a minimum helps to ensure low-cost unit production.
Merkur Excellence Operational Services
Over the years, Merkur has developed a refined and inclusive method of maximizing productivity, profits, and efficiency in manufacturers, and to this day, we are advising worldwide businesses on how to improve efficacy in every part of their assembly lines. From concept development, to program implementation, to data collection and management, our team can help your industrial business excel in today and tomorrow’s markets.
Start here.